Understanding High Pressure Die Casting Products and Their Impact on Modern Manufacturing
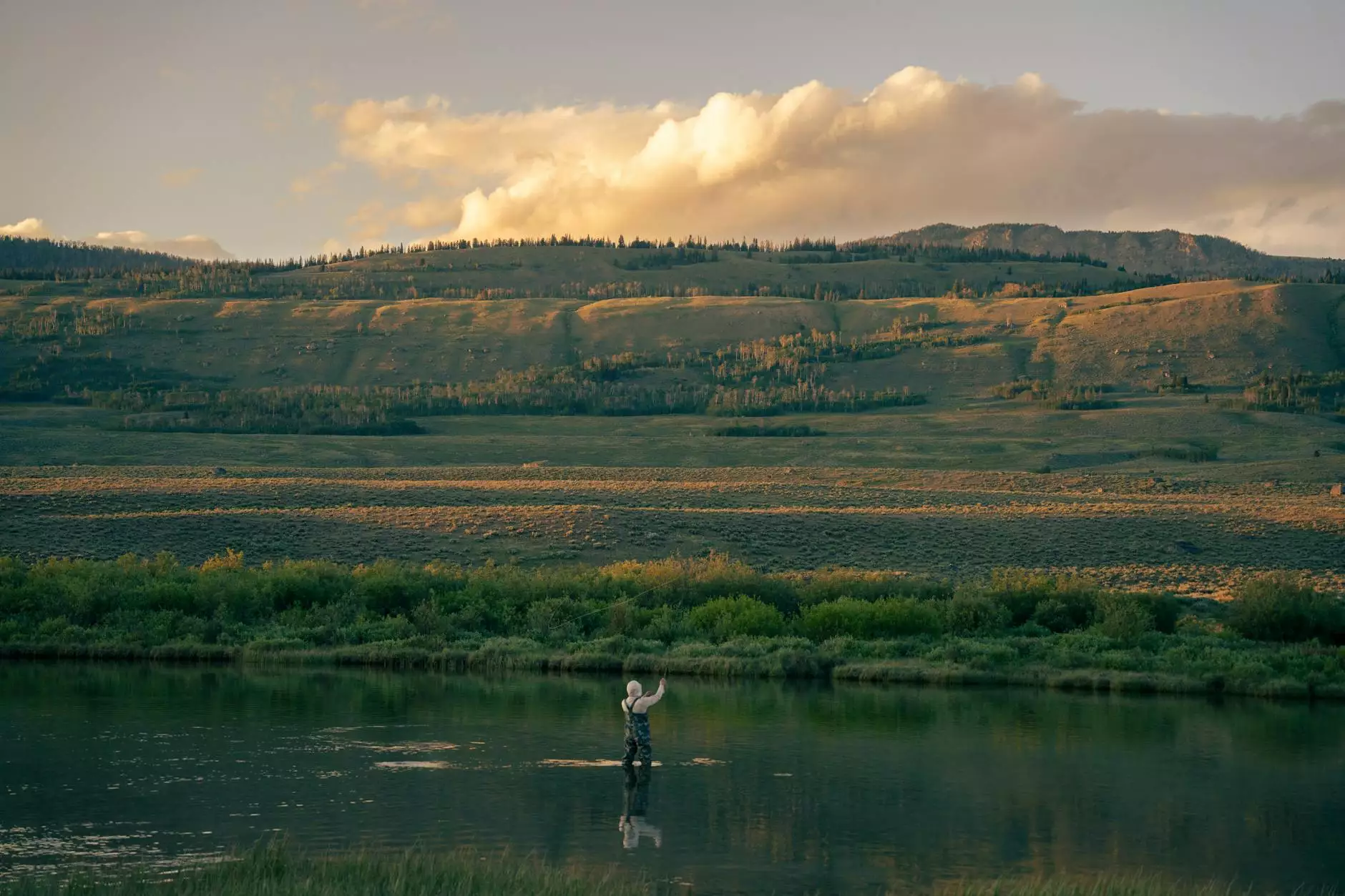
High pressure die casting products represent a revolutionary process in metal fabrication that has transformed various industries by providing precise, efficient, and cost-effective solutions. The evolution of this technology has paved the way for enhanced production methods, culminating in high-quality products that meet the rigorous demands of today's marketplace. In this article, we will delve into the intricacies of high pressure die casting, its advantages, applications, and why it is pivotal for businesses involved in metal fabrication like DeepMould.net.
The Basics of High Pressure Die Casting
High pressure die casting is a method where molten metal is injected into a mold under high pressure. This technique allows for the production of intricate shapes and high-volume parts with exceptional surface finishes. The process involves several key steps:
- Melting: The metal, often aluminum or zinc, is melted in a furnace.
- Injection: The molten metal is then injected into a steel mold at high pressure.
- Cooling: Once filled, the metal cools and solidifies, taking the shape of the mold.
- Ejection: Finally, the mold opens, and the finished part is ejected.
Key Characteristics of High Pressure Die Casting Products
The products created through this process exhibit several distinctive characteristics that set them apart from other manufacturing methods:
- Precision: High pressure die casting allows for tight tolerances and intricate designs.
- Surface Finish: The finished products possess a superior surface quality, often requiring little to no further finishing.
- Strength: The process ensures that the products are strong and durable, making them suitable for various applications.
- Cost-Efficiency: High production speed and minimal waste contribute to a lower cost per unit.
Applications of High Pressure Die Casting Products
The versatility of high pressure die casting products allows their application across numerous industries, including:
Automotive Industry
In the automotive sector, components such as engine blocks, transmission cases, and various structural parts are produced using die casting. The lightweight yet robust characteristics of these products contribute to improved fuel efficiency and performance.
Aerospace Industry
High pressure die casting is crucial in the aerospace industry as well. Components like aircraft frames and engine parts must meet stringent weight and safety standards. The precision and strength of die cast products make them ideal for such applications.
Consumer Electronics
Consumer electronics also benefit from this technology. Items like casings for laptops and smartphones are often made using high pressure die casting, combining aesthetics with strength and durability.
The Advantages of Choosing High Pressure Die Casting
The advantages of utilizing high pressure die casting products extend beyond their functional benefits. Here are some compelling reasons why businesses should consider this manufacturing approach:
Enhanced Production Rates
The die casting process is designed for high-speed production, allowing manufacturers to produce a large number of intricate parts within a short timeframe. This efficiency is particularly beneficial for industries requiring large-scale production.
Reduced Waste and Environmental Impact
With high pressure die casting, the amount of material wasted during production is significantly minimized. Additionally, the reuse of scrap metal ensures that the environmental impact is kept to a minimum, aligning with modern sustainable practices.
Flexibility in Design
Another significant advantage of high pressure die casting is the flexibility it offers in terms of design. Manufacturers can create highly complex shapes that might be impossible or too costly to achieve through other methods.
Challenges in High Pressure Die Casting
While there are numerous benefits to high pressure die casting, it is essential to acknowledge some challenges. Understanding these can help businesses make informed decisions:
- Initial Tooling Costs: The upfront costs for molds can be high, though they are amortized over large production runs.
- Material Limitations: Typically, non-ferrous metals like aluminum and zinc are used, which may limit applications for certain industries.
- Sensitivity to Process Variables: The quality of the cast product can be affected by changes in process conditions, necessitating stringent quality controls.
Quality Control in High Pressure Die Casting
To ensure the production of high-quality high pressure die casting products, rigorous quality control measures are essential. Some of these measures include:
Automated Inspection Systems
With the advancement of technology, many manufacturers now employ automated inspection systems that utilize advanced sensors and cameras to accurately assess the quality of each cast product.
Non-Destructive Testing (NDT)
NDT methods such as ultrasonic testing and X-ray inspection are employed to detect internal defects without damaging the products. This ensures maximum reliability and safety for the end-users.
The Future of High Pressure Die Casting
The future of high pressure die casting products is promising, with ongoing advancements in technology and materials. Innovations such as:
- 3D Printing: The integration of 3D printing technology with die casting can streamline the prototyping process, allowing for faster development and iteration of designs.
- Smart Manufacturing: The rise of Industry 4.0 will further enhance the efficiency and precision of die casting processes through data analytics and IoT.
- New Alloys: Research into new alloy compositions may unlock new applications and enhance the performance of die-cast products.
Conclusion
High pressure die casting products play a crucial role in modern manufacturing, offering an array of benefits that appeal to various industries. By selecting this efficient manufacturing method, businesses can achieve high-quality, precise components that meet the rigorous demands of their respective markets. As the technology continues to evolve, companies like DeepMould.net stand at the forefront, ready to provide superior metal fabrication solutions. Embracing high pressure die casting not only enhances production capabilities but also positions companies for sustainable growth and innovation in an ever-competitive landscape.
Why Choose DeepMould for High Pressure Die Casting Solutions?
With a commitment to excellence, DeepMould is your trusted partner in high pressure die casting. Our expertise in the metal fabrication industry, combined with state-of-the-art technology, ensures that we deliver:
- Customized Solutions: We understand that each project is unique. Our team works closely with clients to develop tailored solutions that meet specific needs.
- Expert Guidance: Our experienced engineers provide insights and recommendations to optimize designs for manufacturing.
- On-Time Delivery: We pride ourselves on meeting deadlines without compromising quality.
Looking for exceptional high pressure die casting products? Contact DeepMould.net today to discuss your project needs.